There are already many articles on the topic of smart factory.
In this article, I will try to simplify it a little bit, starting off with a brief overview of the history of industrial revolutions, introduction of what smart factory is, and then talk more in detail about its characteristics, technologies and solutions necessary to give what is mere flesh (physical, hardware) a soul (cyber, software).
Industrial revolutions then, and now
To fully grasp what smart factory is and where it’s headed, we must first understand the history of manufacturing.
It all began with the First Industrial Revolution, which introduced machines to factories and farms in the mid-18th century. In the past 250 or so years, manufacturing has evolved from handwork to machines like the spinning jenny, from the rise of machines to automobiles which were first introduced to the general public by Henry Ford in 1908, and from new inventions to digital technologies that made semiconductors, computers and the Internet possible.
It wasn’t until decades ago that the fourth industrial revolution brought smart manufacturing technologies which emphasise on automation with the use of Internet of Things (IoT).
Smart factory, and why it matters to you
We will briefly explain what a smart factory is and dig deeper into some of its characteristics and the key technologies necessary to make it smart.
What is smart factory?
A smart factory is a shop floor that adopts smart manufacturing. Smart manufacturing is manufacturing that uses various technologies and solutions – like AI and IoT – arising from Industry 4.0 to optimise the production process.
By using smart manufacturing technologies, smart factories produce more goods with less errors, down-time and human efforts, as opposed to traditional factories that rely on manual processes prone to human errors and production delays.
What are the notable characteristics of a smart factory?
A smart factory has the following characteristics:
- It’s digital. We understand more about our factory when things inside it are ‘connected’ (networked) to one another. Sensors and other IoT devices are used to collect data about the equipment and machines. Such data is either stored in an on-premise server or transmitted to the cloud via WiFi or other wireless network protocols for further analysis. This sensor-driven capability helps increase manufacturers’ awareness of what’s happening in the factory.
- It’s intelligent. We make better decisions when the factory is able to tell us more about itself. For example, when a digital twin, the virtual counterpart of a physical object, receives data about the asset’s performance, it will run simulations in a digital world to diagnose performance issues and generate future predictions, offering valuable insights for predictive maintenance (PdM). IT companies like Siemens and IBM already use digital twins to increase productivity and shorten development cycles.
- It’s automated. We produce goods faster with less human effort involved. In manufacturing, automation is driven by technologies such as machine learning, AI and big data. When given the insights that tell us the performance, energy output and temperature of a machine, manufacturers are able to figure out patterns and make rules so should a failure be likely to happen, the machine would know what to do and take action automatically to avoid production down-time and delays.
What are the key technologies used to build a smart factory?
Industry 4.0 is powered by technologies such as the Internet of Things, big data, machine learning and digital twins – all these buzzwords are attached to the topic of smart factory.
Here is a short explanation of what each term means for the factory of the future:
- The Internet of Things (IoT). The Internet of Things allows devices to ‘talk’ to each other. When physical objects embedded with sensors, cameras and other devices are connected to the internet, they can gather data of the equipment and machines inside a manufacturing factory, analyse it, and use the resulting insights to optimise operations.
- Artificial Intelligence (AI). Artificial intelligence tries to make machines ‘think’ like humans. This concept of intelligence demonstrated by a machine after digesting the data collected by IoT devices plays a big role in predictive maintenance (PdM). For example, AI-enabled systems can make the decision to send alarms early to forecast failures.
- Machine Learning (ML). Machine learning is a ‘method’ (or application) of artificial intelligence. It trains machines to learn from experience by finding patterns in data and therefore enables them to make decisions to predict possible futures. A well-educated machine can automatically send alarms when detecting failures likely to occur.
- Big Data. Big data is a massive amount of data. It is information fed to the AI for it to learn through trial and error, and eventually grow and become smarter. The more data that is given, the more accurate the algorithms for making judgement might become.
- Digital Twin. Digital twins help people understand the present, and future of physical things. They are the digital counterparts of physical objects such as cars, buildings and machines. When data collected by the sensors embedded in these objects is mapped onto these virtual models, they can tell manufacturers how these objects are performing in the real world, and even run tests of different scenarios virtually without having to build physical prototypes.
- Robotics. Robotics assist humans in their everyday life. In manufacturing, applications of robotics technology include robotic arms taking on repeated, routine tasks in a production line and AGVs (Automated Guided Vehicle), helpers in transporting heavy materials from one place to another. The importance of robotics, robotic automation to be more specific, and its role in a smart factory will be discussed in another article.
In short, these data-driven technologies serve as the backbone of a smart factory. When used together, they enable machines to communicate to one another, think on their own, and become smarter for a more automated and efficient manufacturing process.
A couple solutions to kick off your smart factory
TECHDesign is a one-stop hardware development platform that offers solutions and services to help you develop your smart solutions.
To stay on top of what’s going on in your factory, the first step in making it smart, we picked a couple IoT control and monitoring solutions:
- Industrial Energy Monitoring System is an easy-to-install, customisable system where you can monitor the electrical consumption, abnormal status, unexpected downtime and more of your equipment by looking at real time data accessible on your PC, laptop, or mobile devices. A management system like this one not only detects breaks-ins, fires and other abnormalities but also sends alarms when one does occur;
- Warehouse Monitoring System allows you to check environmental parameters such as temperature, humidity and air quality in real time;
- Lighting Control System gives you remote control of indoor lights and provides analysis on how much power is consumed;
- Battery Monitoring System is particularly important if your factory runs a 24/7 daily schedule. It will periodically measure the voltage, current, temperature and the internal resistance of each battery to prevent failure;
- Wireless gateway for data collection and control bridges your computer and all the other internet-enabled machines so they operate under the same, shared wireless connection. This way, data is collected securely in a central place for better management. You can learn more about gateways here;
- RFID tag with a RFID reader or industrial tablet make a perfect combo in asset tracking and inventory control. When these tags are installed and scanned, you no longer need to count your items as they’re all accounted for.
The utilisation of all these mentioned IoT solutions allows you to keep your factory running effectively and efficiently, producing more goods with less downtime and errors.
What’s next after Industry 4.0?
In this article, we’ve explained the characteristics of a smart factory, the key technologies that drive it, and solutions from TECHDesign that can quickly help you build this new model of factory born in the latest industrial revolution, Industry 4.0.
What comes next after the fourth industrial upheaval? The answer is Industry 5.0.
Industry 5.0 that focuses on resiliency and sustainability
You probably have already read many opinions on what Industry 5.0 is, and what it will bring to manufacturing in the next decade.
So here I’m tackling it from a different viewpoint: Industry 5.0 is the next industrial revolution that extends, or complements, Industry 4.0 with elements such as resiliency and sustainability.
What is a resilient smart factory? In the future, smart factories located in different parts of the world could respond quickly to external impacts such as the COVID-19 crisis. By connecting all the systems and their corresponding data, smart factories could automatically order from different supplies and find new ones to avoid domestic or worldwide supply chain shortage, as opposed to operating on their own as standalone factories like they do now.
Being sustainable means doing our part for Earth and the future generations. A sustainable smart factory could contribute its share by rolling out cleaner, healthier goods. That is, things in your everyday life – from PCs to cars to coffee machines – could be produced by recycling waste from the same products and generating such waste into energy while minimising CO2 emissions.
Industry 5.0 will arrive soon. To simply stay competitive, manufacturing companies like yourself need to act now. TECHDesign is and will be here to help you get ready for such a resilient, and sustainable industrial era.
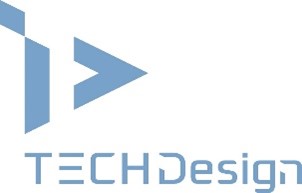