No matter where your enterprise might be on its digital transformation journey, there is always something that can be done to add additional automation to your workflows.
From digitising and automating previously repetitive and time-intensive manual and paper-based jobs to adopting new, highly advanced intelligent workflow automation technologies powered by IoT cameras and sensors, the real benefits of workflow automation depend upon the software platform that underpins it.
Nevertheless, enterprises continue to make the same mistakes when implementing process automation, making it more difficult for staff to reap the benefits of the technology and struggling to procure the right workflow automation software to enable them to achieve this.
Often, they are beholden to legacy software and systems not built to solve the problems they face today and cope with new problems they will face tomorrow.
Switching up the software procurement mindset
Automating processes and workflows is at the heart of business success in any modern enterprise. Business leaders understand the benefits of embracing and accelerating digitalisation: cutting costs, improving productivity and service levels, streamlining their staff’s day-to-day workflows and processes, and more. However, there needs to be a fundamental mindset change in how enterprises procure and implement the right workflow automation software. And, more importantly, how they find a software partner that understands their needs and can grow with them.
Instead of buying ‘point solution’ off-the-shelf style apps and software to solve specific micro-level workflow issues and problems, businesses need to think instead about investing in the development of a flexible and adaptable software platform. A configurable platform can integrate easily with legacy tech and be adopted and used to solve almost any workflow automation requirement.
Subsequently, enterprises should use configurable solutions to avoid over-complicating the process, creating a flexible tech stack that can address almost any problem. This allows each new workflow automation requirement to become another process within a single software solution.
The adoption of process management apps
Process management apps ensure users stick to organisation processes, improve them, and verify that they have been followed.
In the grocery retail sector, process management apps are used in the majority of UK supermarkets to help retailers digitise, automate, and improve efficiencies around previously labour-intensive jobs, from digitally updating cleaning and safety logbooks to automating regular hot food temperature checks or store safety and security checks, and much more.
Such apps initially help the business move away from numerous outdated manual and paper-based safety, cleanliness, and compliance processes. These processes are then gradually converted into simple workflows that can be done on the go. Apps trigger automated corrective actions, meaning that as soon as in-store issues are recognised, managers are immediately aware of it, and a job is assigned to resolve the issue.
For instance, the digitalisation of in-store logbooks allows retailers to cut the number of daily checks down and reduce the number of trips and slips claims made against a company. This saves businesses millions of pounds while providing management and employees with an invaluable tool to empower them to do their jobs better.
A switch towards IoT and dynamic facilities management
If the first stage of smarter workflow automation is digitising and automating traditional paper-based manual processes, the next level for enterprises is a shift to advanced forms of automation powered by connected IoT devices, such as sensors and cameras, which are used to automatically trigger jobs and workflows.
Across the facilities management (FM) sector, digitised facilities management systems enable smarter operations such as dynamic cleaning and maintenance, whereby IoT sensors allow estate managers to monitor the cleanliness and conditions of offices, stores, schools, hospitals, and other ‘smart’ buildings remotely and automatically trigger alerts when and where cleaning or maintenance or any other corrective actions are needed.
The importance of identifying and mapping workflows for automation
Some enterprises believe that most business processes are unchanged when most workflow processes can withstand change and improve once automated. However, before adjusting to automated processes, it is important to identify the areas where it can have the biggest impacts, including simple and repetitive tasks prone to errors and hampering productivity.
Once the desired areas of automation are identified, workflows must be mapped before implementation. Mapping workflows enables enterprises to establish what is required and whether individual elements can operate with automation software.
Before implementing automation software, enterprises must be willing to adapt workflows and examine each process to allow teams to achieve goals as they attempt to implement automation.
Selecting the right automation partner
When looking to the future of workflow automation, digitalisation, and services such as dynamic cleaning and maintenance or food quality audits are the next logical steps for the FM and contract catering industries.
Businesses need to take a much longer-term view of their requirements for workflow automation, find a software partner they can collaborate with, and a platform with built-in flexibility so it can move as their requirements move.
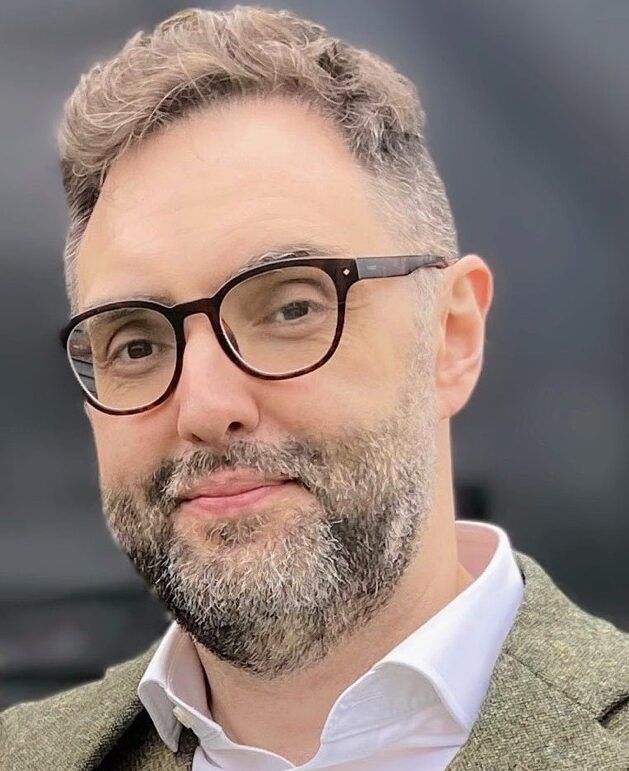
Phil Meyers is COO of Mobile Workforce Management Software mpro5.