As 2025 nears, Lucas Garcia, Principal Product Manager for Deep Learning at MathWorks delves into the AI trends expected to shape engineering
As we look ahead into 2025, AI will continue to offer engineers new ways of enhancing precision, efficiency, and adaptability across various domains. As engineers continue their work with AI, they should ensure that they are covering advancements in the following key areas: generative AI, verification & validation, Reduced Order Models (ROMs), and control system design. These trends will reshape engineers’ ways of working in 2025 and in the years to come.
Trend #1: GenAI Moves onto block diagrams, 3D models, and flow charts
While the initial focus on text-based GenAI continues to influence software-centric workflows, its impact on engineering tools with higher-level abstractions is lagging. In 2025, we expect continued progress in applying GenAI to “no code” engineering tools such as block diagrams, 3D models, and flow charts.
These tools enable engineers to graphically represent complex systems, effortlessly edit components, and manage the inherent complexity. Further, they are essential to engineers’ productivity and validate the engineers’ confidence in system-level performance. Integrating GenAI with these tools will further increase their productivity while keeping the interfaces familiar to end users. More tools in this space will integrate AI copilots that can understand engineering models and assist in their design and management.
Trend #2: Leveraging verification and validation for AI compliance
Industry governing bodies are introducing AI compliance requirements, frameworks, and guidance as the integration of AI into safety-critical systems in automotive, healthcare, and aerospace applications accelerates. In response, engineers must prioritise Verification and Validation (V&V) processes now to ensure their AI components are ready for deployment under all conditions and meet potential reliability, transparency, and bias compliance standards.
V&V is crucial for verifying the robustness of deep learning models and detecting out-of-distribution (OOD) scenarios, particularly in safety-critical applications. Robustness verification is crucial because neural networks can misclassify inputs with minor, imperceptible changes, known as adversarial examples. For instance, a subtle perturbation in a chest X-ray image might lead a model to incorrectly identify pneumonia as normal. Engineers can provide mathematical proof of a model’s consistency and test these scenarios using formal verification methods, such as abstract interpretation. This process enhances the model’s reliability and ensures compliance with safety standards by identifying and addressing vulnerabilities.
Out-of-distribution detection is equally important, as it enables AI systems to recognise and appropriately handle unfamiliar inputs. This capability is vital for maintaining accuracy and safety, especially when unexpected data leads to erroneous predictions. The ability to discern between in-distribution and out-of-distribution data ensures that AI models can defer uncertain cases to human experts, thereby preventing potential failures in critical applications.
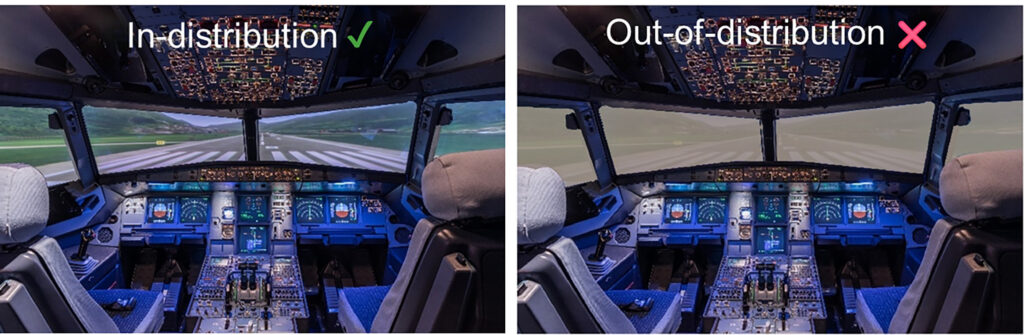
Focusing on V&V allows engineers to comply with AI frameworks and standards while advancing product development within their industry. A proactive compliance approach ensures that AI systems are reliable, safe, and ethically sound, maintaining a competitive edge in a rapidly evolving landscape.
Trend #3: The rise of AI-based Reduced Order Models
The use of AI-based Reduced Order Models (ROMs) is expected to grow, driven by advances in AI technology and computational power. Engineers leveraging these models will enhance system performance and reliability, as well as the efficiency and efficacy of system design and simulation.
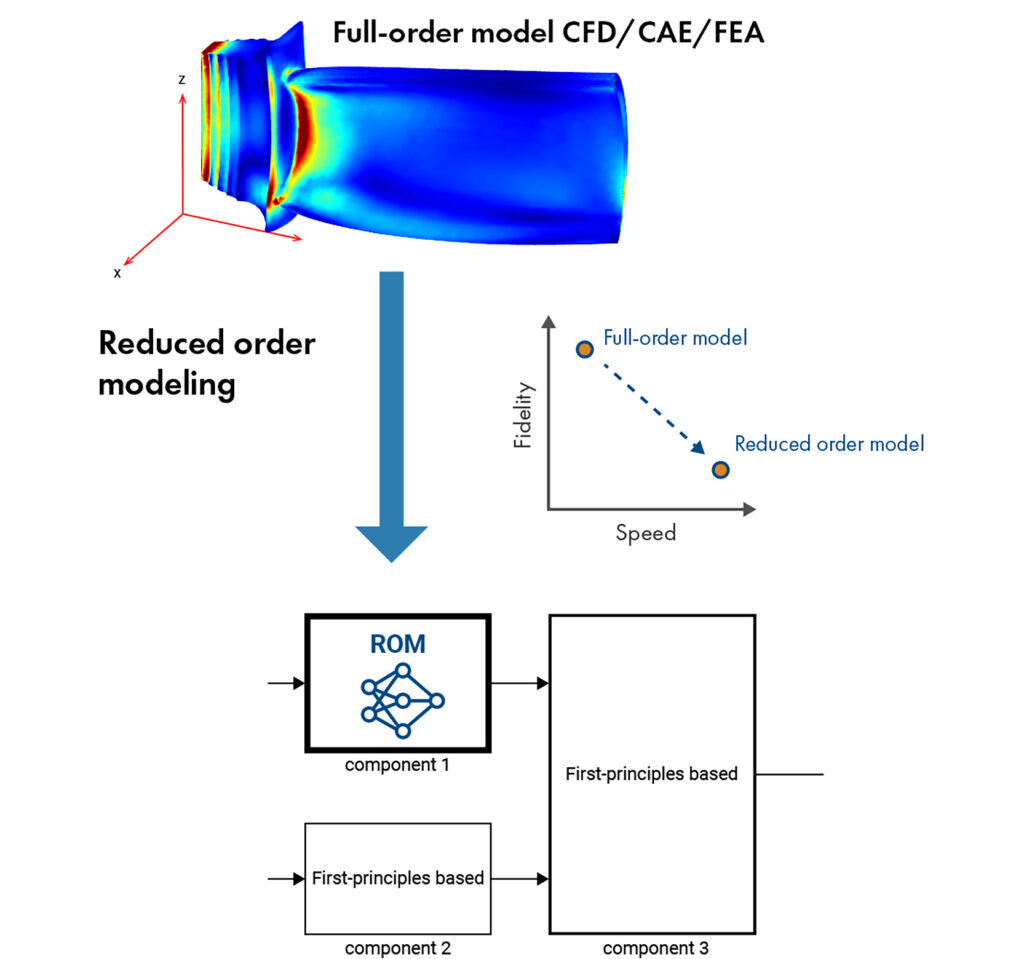
The primary driver behind this shift is the need for engineers to manage increasingly complex systems while maintaining high levels of precision and speed. Traditional computer-aided engineering (CAE) and computational fluid dynamics (CFD) models are accurate but computationally heavy and suboptimal for real-time applications. AI-based ROMs address this by cutting computational demands while maintaining accuracy. Engineers can use these models to simulate complex phenomena more quickly, facilitating faster iterations and optimisations.
Furthermore, AI-based ROMs’ highly versatile ability to adapt to varying parameters and conditions enhances their applicability across different scenarios. This adaptability is particularly valuable in the aerospace, automotive, and energy fields, where engineered systems often involve intricate physical phenomena that require detailed modelling and simulation.
For example, engineers designing and testing aircraft components, such as wings or engines, can simulate aerodynamic properties and stress factors more efficiently, allowing engineers to iterate and optimise designs quickly. Additionally, AI-based ROMs can adapt to various flight conditions, making them versatile tools for testing multiple scenarios using the same model. This capability accelerates the development process, reduces costs, and enhances the reliability of the final product.
Trend #4: AI breaks enhances complex system control
AI’s continued integration into control design will transform the field, particularly in managing complex systems and embedded applications. Traditionally, control system design relied on first-principles modelling that required deep knowledge and understanding of the system.
Data-driven modelling was largely limited to linear models that are valid only in a small part of the design envelope. AI is transforming this landscape by enabling the creation of accurate nonlinear models from data. This enables the creation of highly accurate models that combine first principles and data and are valid over the entire operating range. This advancement allows for better control of complex systems.
Simultaneously, the growing computational power of microcontrollers is facilitating the embedding of AI algorithms directly into systems. This integration is particularly impactful in the consumer electronics and automotive industries, where highly responsive systems are becoming the norm. For instance, AI is embedded in power tools to monitor and react to environmental changes, such as sudden material density shifts that could pose safety risks. These tools use embedded AI to autonomously adjust their operation, enhancing safety and performance.
The convergence of AI with complex system control and embedded systems ushers in an era of more robust, adaptive, and intelligent control design. Engineers can now create systems that learn and adapt in real-time, providing unprecedented precision and efficiency. This creates an environment where AI-driven solutions address traditional control problems, paving the way for smarter, more integrated systems across various engineering domains.
Engineers should be excited about AI’s proliferation and potential. The fusion of physics insights with AI models will enhance transparency and adaptability, reducing the “black box” nature of traditional approaches, while the democratisation of AI tools enables engineers to access advanced capabilities more easily. These developments will elevate AI’s role in engineering and enable professionals to build better engineered systems more rapidly and effectively.
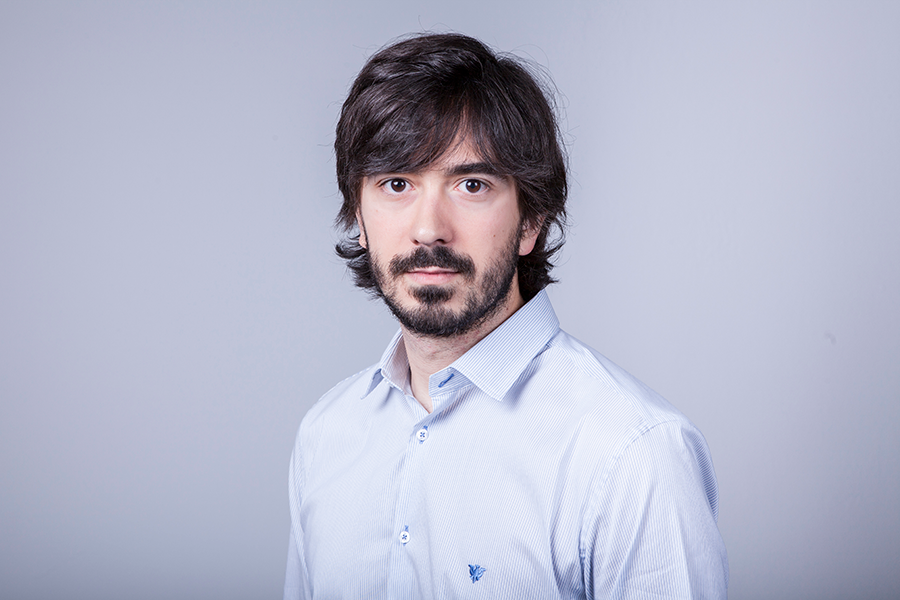
Lucas García is a Principal Product Manager for Deep Learning at MathWorks with more than 15 years of machine learning experience and research in the computer software industry. He works with customer-facing and development teams to define, develop, and launch new capabilities and applications that meet customer needs and market trends in deep learning.
Author: Lucas Garcia, Principal Product Manager for Deep Learning at MathWorks
There’s plenty of other editorial on our sister site, Electronic Specifier! Or you can always join in the conversation by commenting below or visiting our LinkedIn page.