Fabio Zaniboni, Founder and Chief Executive Officer at BubblyNet writes about how Luminaire Level Lighting Control is the backbone of IoT
As the manufacturing and logistics industries move towards automation, efficiency, and sustainability, a new technology is emerging as the backbone of smart facilities—Luminaire Level Lighting Control (LLLC). Traditionally, lighting has been seen as a basic necessity, but with LLLC, it is transforming into a wireless communication network that enables energy savings, HVAC optimisation, space utilisation tracking, and predictive maintenance.
Beyond energy rebates: LLLC as an IoT backbone
LLLC refers to the integration of motion sensors and wireless communication nodes into each luminaire (light fixture). Initially driven by energy rebates and incentives, LLLC has evolved into a foundational infrastructure for smart facilities. Unlike traditional lighting control systems that rely on centralised controllers and complex wiring, LLLC uses a wireless mesh network (WMN) to provide real-time data and decentralised decision-making.
An WMN is a system where each luminaire communicates directly with its neighbours, creating a self-healing and adaptive network. This approach eliminates the need for extensive cabling and allows seamless integration of new sensors and devices as technology evolves.
Ford’s Rouge Complex in Michigan, one of the largest automotive manufacturing plants in the US, has adopted LLLC with wireless mesh networking to improve energy efficiency and operations. By embedding motion sensors and wireless nodes into their LED lighting, the facility has reduced lighting-related energy costs by 50% while also enabling real-time monitoring of occupancy and machine activity. The data collected is used to adjust HVAC loads, optimise workflow layouts, and predict maintenance needs, making the entire plant more efficient.
HVAC control: the largest opportunity for energy savings
In manufacturing and logistics facilities, HVAC systems account for a significant portion of energy consumption. Traditionally, HVAC control relied on wired BACnet networks, but with the rise of wireless BACnet and Bluetooth Mesh, HVAC optimization is becoming easier to implement and more cost-effective.
With LLLC-integrated motion sensors, lighting systems can detect occupancy and automatically adjust both lighting and HVAC settings. If an area of a warehouse or production floor is unoccupied, the system can dim the lights and lower the HVAC output, reducing energy waste.
Amazon, known for its highly automated distribution centres, has implemented LLLC-integrated HVAC control in its fulfillment facilities. Sensors embedded in luminaires track occupancy patterns, air quality, and temperature changes, allowing for real-time HVAC adjustments. This system has led to a 30% reduction in HVAC-related energy costs and has also improved worker comfort by dynamically adjusting airflow in high-traffic areas.
By integrating LLLC with HVAC systems, manufacturers and logistics operators can achieve substantial cost savings, reduce carbon footprints, and improve employee working conditions.
Motion sensing and people counting: beyond just lighting control
While LLLC’s embedded motion sensors are primarily used to control lighting levels, their capabilities extend far beyond that. These sensors can be leveraged for people counting, HVAC adjustments, and predictive maintenance.
By analysing motion patterns and equipment usage, facilities can anticipate when machines need servicing, reducing downtime. Cleaning schedules can be adjusted dynamically based on actual space usage, rather than fixed schedules, optimising operational expenses (OPEX).
Simple-to-implement facilities monitoring and control
One of the biggest advantages of LLLC-based wireless mesh networks is their ability to simplify remote monitoring and control of manufacturing and logistics facilities. Because each luminaire acts as a sensor and data node, the granularity and density of data collection are unparalleled.
Additionally, Edge computing at the luminaire level reduces the amount of data that needs to be sent to the Cloud, making Cloud integration lean and cost-effective. This enables sophisticated single-pane-of-glass dashboards.
Walmart has implemented LLLC-based smart monitoring in its high-volume distribution centers to improve efficiency and reduce costs. Their system:
- Tracks lighting, HVAC, and equipment status in real time
- Uses Edge AI processing to automate adjustments based on worker movement and environmental conditions
- Provides facility managers with remote monitoring dashboards, allowing them to optimise operations across multiple locations with minimal oversight
The result? A 20% reduction in energy costs, optimised warehouse space usage, and a significant reduction in maintenance costs due to predictive analytics.
Conclusion
Luminaire Level Lighting Control has evolved from a simple energy-saving tool into a critical infrastructure component for smart manufacturing and logistics facilities. By acting as a wireless mesh backbone, LLLC enables scalable sensor integration, real-time monitoring, and operational cost reductions.
From HVAC optimisation and motion sensing to predictive maintenance and space utilisation tracking, LLLC is transforming industrial operations.
As technology continues to evolve, facilities that invest in LLLC today will remain competitive, sustainable, and highly efficient in the years to come.
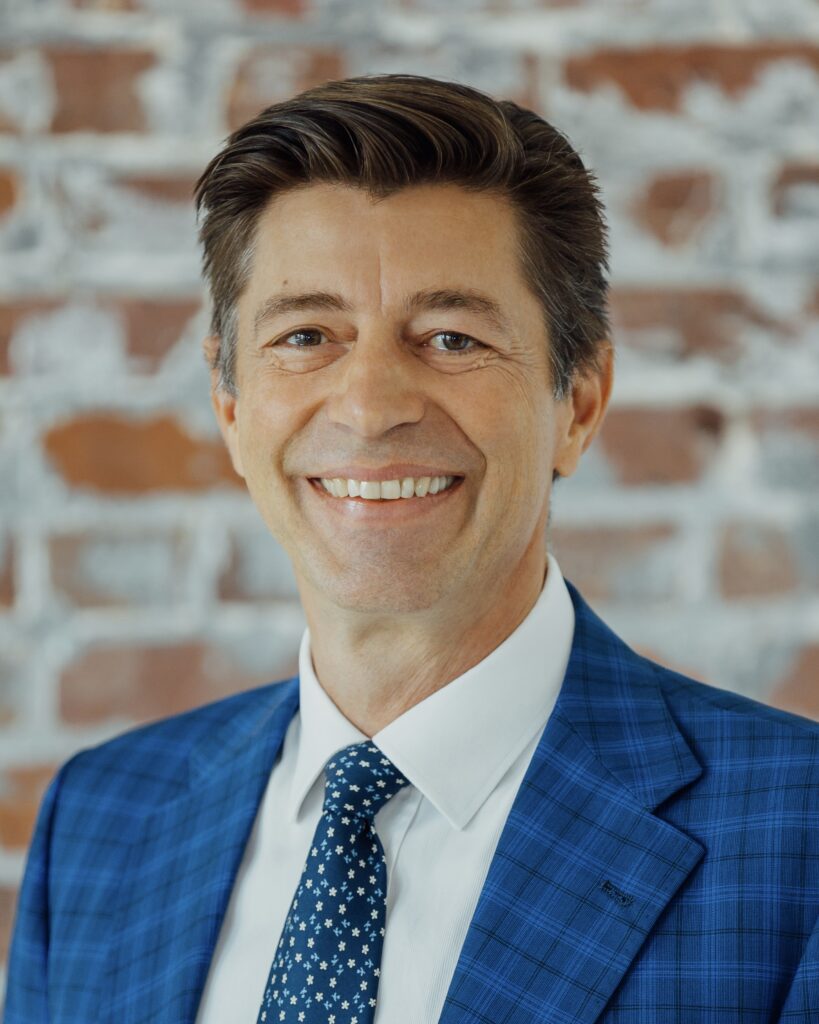
Fabio Zaniboni is a technology leader with over two decades of experience in the Internet of Things (IoT), digital transformation, and sustainable innovation, particularly in the lighting industry. His career, including roles at Emerson Electric and Comau Robotics, has given him a global perspective and market insights. Leading an R&D team, Fabio integrates advanced technologies to enhance building efficiency, sustainability, and user experience.
There’s plenty of other editorial on our sister site, Electronic Specifier! Or you can always join in the conversation by commenting below or visiting our LinkedIn page.