Hyperautomation may have begun as a tech buzzword but it is now influencing leaders as a strategic technology priority, with many business leaders seeing the potential value in leveraging robotic process automation (RPA), AI and ML (machine learning) to transform legacy processes and improve operational efficiency. In an era where all digital transformation initiatives seem to take precedence, however, finding where to begin is no simple task. As many manufacturers are putting more efforts toward shaping their digital transformation strategies, being more proactive and enabling data-driven decision making, increasing data accuracy in the imperfect world of manufacturing remains as a challenge.
According to Gartner, hyperautomation “is a business-driven, disciplined approach that organisations use to rapidly identify, vet and automate as many business and IT processes as possible”. It is increasingly becoming a vital part of organisations’ digital transformation roadmaps as a means to achieving digital resilience and agility.
As manufacturing organisations dive headlong into hyperautomation, it is critical for leaders to plan strategies to accelerate processes and deliver value without getting lost in the current technology weeds. After several years of planning and implementing digital transformation and smart manufacturing initiatives, how far do organisational benefits currently extend?
The last few years have seen this trend accelerate. The pandemic forced businesses to look toward hyperautomation as humans complied with lockdowns. With the business ecosystem operating in a distributed manner, hyperautomation eases the burden that repetitive processes and legacy infrastructure put on an organisation and its resources. Hyperautomation means that an organisation is more streamlined, leading to reduced costs and a stronger competitive position.
Critical growth driver
Even with other recent events and disruptions like supply chain issues and staffing shortages, 60% of executives say digital transformation is their most critical growth driver. Though digital transformation can be difficult as it requires organisations to change culture and traditional structures, digitalisation is crucial to industry’s ability to increase efficiency in production and drive further growth of the enterprise.
While disruptions and challenges have stalled out, major challenges with the supply chain and increased operational costs can persist through digital transformation initiatives. Of course, it’s not realistic to expect to eliminate longstanding challenges in such a short span of time. Currently, many leaders share common challenges in justifying ROI for smart manufacturing investment using end results. While having access to data is now certainly realistic for most organisations, building visibility into real-time data across multiple databases at the organisation remains as a huge roadblock.
Repetitive manual tasks
Siloed data and unstructured data sets, multiple versions of pieces of digital content without the ability to track them – such as sales contracts and datasheets – and the inability to streamline business processes across different applications and departments are just some of the unimproved roadblocks that are still managed manually. When envisioning the end-results of our digital transformation efforts, it may not be what leaders were expecting: it is a common reality that employees are still spending hours on repetitive manual tasks.
As organisations begin the journey of hyperautomation, a structured foundation allows organisations to not only save tremendous amounts of time on daily business processes but also allows leadership to have a 360-degree view of real-time databases and business progress organisation-wide.
Cloud-based solutions can provide much easier solution implementations without requiring dedicated employees or specific skill sets. More technology vendors are offering out-of-the box and low-code options to connect core applications, which takes much of the heavy lifting from organisations, especially ones in complex industries like manufacturing. With low-code powering much of today’s hyperautomation efforts, organisations can explore the potential of technologies like AI to redefine how technologies integrate. According to a recent study by SME and Laserfiche, increasing overall process effectiveness and enabling data-driven decision making are the top priorities for organisation’s process integration and digitalisation journeys.
Banish the bottleneck
Eliminating bottlenecks between disparate automated processes to create an end-to-end solution accelerates high-level initiatives and creates quick results. In the same SME and Laserfiche survey, the two-thirds of respondents indicated that their communications are a combination of internal and external, indicating that legacy methods of communication are not sustainable, raise security concerns and are inefficient.
The simple yet effective approach of centralising processes and information in a cloud-based repository with features that help eliminate repetitive human tasks, mitigate errors and avoid delays will lift a huge barrier to redefining digital transformation. As organisations increase efforts to scale existing automation efforts and legacy business processes to create more sustainability in operations, developing an end-to-end structure of automations supports organisations in creating clearer top-to bottom strategies, and measuring productivity improvement that will help justify ROI initiatives – yet another high priority for manufacturers undergoing digital transformations.
Automating the capture of unstructured data, automatically routing and storing critical documents, and managing the life cycle of content can simplify the way people and departments collaborate, decrease operational costs and support better resilience for businesses.
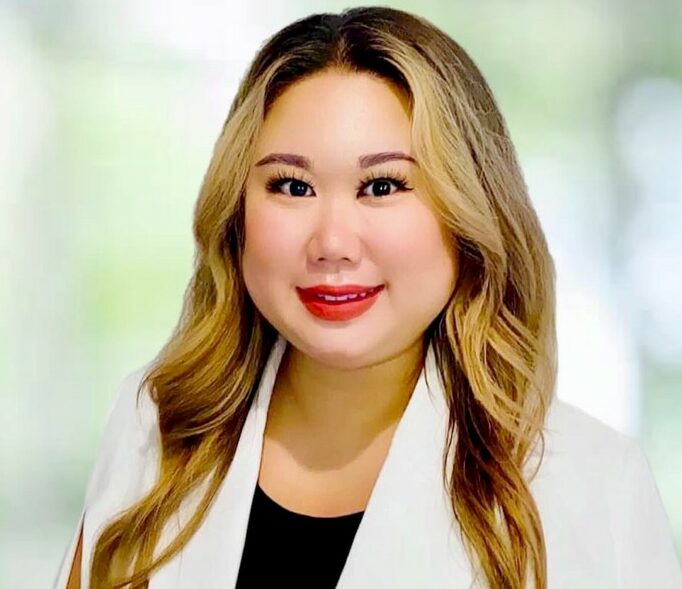
Grace Nam is Strategic Solutions Manager for Manufacturing at Laserfiche.