The global mobile robotics market was valued at $25 billion in 2024 and is expected to grow at 20.7% CAGR by 2030, according to Grand View Research. However, in order for this market to be allowed to continue to grow, the industry must first solve one glaring issue: the challenge of creating software that is easy to use.
This is the exact challenge NODE Robotics have taken on, a five-year-old software startup specialising in mobile robotics and based in Germany. Dr. Stefan Dörr-Laukien, CEO and Co-Founder of the company delivered a talk at Advantech’s Edge Computing Summit in Munich in June, sharing insights into the existing constraints facing mobile robots.
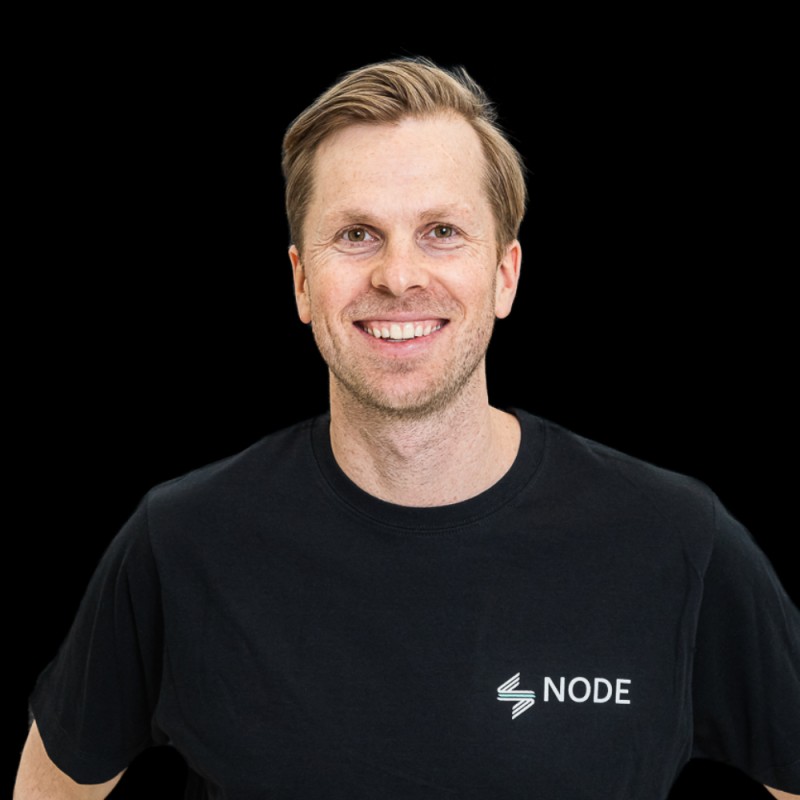
Mobile robots are still considered a niche, because of one major hurdle: it’s difficult to deploy mobile robots. “The main challenge that we currently see in the market … the … solutions are still way too complex to deploy, to install, and thereby [are] limiting the use cases [and] limiting the companies that can actually leverage the potential,” noted Dörr-Laukien.
Deploying mobile robots today, Dörr-Laukien said, companies are frequently faced with a situation where deploying between five and 50 is relatively easy, but scaling is where the challenges arise.
“Delivering to a second customer … is where it gets way more complex,” he said. “This is where you … meet the whole long tail of issues, software failures, hardware failures, of course. And also you meet more and more … new requirements by the end users.”
Companies are therefore faced with two avenues: building or buying a solution.
“Making everything in-house, of course … gives you a lot of room, a lot of independence, moving as fast as you want to tailor … the software and the hardware for your needs,” explained Dörr-Laukien, “but with the downside of long development cycles of high cost and high risk.
“Then there is the option to buy … which gives you a fast go-to-market, but with the current solutions in the market … limits you in a way.”
Breaking down the software
Recognising that both avenues have their pitfalls, NODE Robotics is offering a software platform (NODE.OS), “what we call a make and buy option,” said Dörr-Laukien. “That means we are giving … our customers the opportunity to select different off-the-shelf sensor software packages and combine it with their in-house developments.”
There are four key ingredients making up NODE Robotics’ offering, Dörr-Laukien explained: hardware interfacing and connectors, so the hardware components are plug and play; software interfacing; off-the-shelf robotic components known as their core components; and a DIY environment where customers can build their own packages.
Customers will have different sensors and different compute systems, which means they need to choose the right hardware for their use case. This makes ensuring that the sensors and other hardware components can be connected, even more critical.
Regarding software interfacing, it works with third-party software adapters to provide adapters that automatically connect to different software systems so that the mobile robots operating in a factory can easily connect to a fleet management system, for instance.
The off-the-shelf robotics core components give the robot the capability to autonomously act and operate in an industrial environment.
Finally, leveraging a DIY environment gives their customers the flexibility to build their own packages and behaviours in a mobile robot.
In one example of what this looks like, NODE Robotics worked with a customer that was developing a mobile robot for yarn production; picking up tonnes of yarn from the floor and transporting it to the machines.
“So they built their own hardware in terms of assembling different … form factors … then connected this hardware using the hardware connectors. There was a warehouse management system where the orders for the mobile robots were coming from, they could use our software adapters for that. They used our robotics core [components] … and with our DIY environment, they could build a small behaviour which empowers the robot to hand over the loads and communicate with the machine.”
The off-the-shelf core components are made up of two layers: the robotics layer, which is used for autonomous skills and localisation, so it can determine its position in real time and also utilises fleet coordination orchestration, “because rarely these robots act alone, but rather in fleets from two, five, 10, up to hundreds of mobile robots,” said Dörr-Laukien.
The second layer is the modular software layer that consists of the capabilities needed to manage a fleet of robots.
AI and robotics is emerging
Currently the company has over 50 mobile robot types enabled with its software, and with more than 1,300 working in production.
Its collaboration with Advantech comes into play with the different autonomous mobile robot (AMR) controllers that Advantech provides, to enable its customers to explore advanced features such as sensor fusion.
“This is a future proof setup, because even though AI and robotics … is still early … there are still … [growing] applications … and a lot of customers are coming to us, and they … fear they are missing out,” noted Dörr-Laukien.
In spite of “black and white” discussions revolving around AI – whether it’s here to stay or whether it’s merely a fad, there are three emerging applications the company is working on, helped by the integration of AI technologies to make how the robot perceives the world that much smarter: localisation, obstacle avoidance and obstacle detection, and detecting loads for interaction.
By zeroing in on the need for a modular software solution to support the growing area that is mobile robots, NODE Robotics are primed for the future.
There’s plenty of other editorial on our sister site, Electronic Specifier! Or you can always join in the conversation by visiting our LinkedIn page.