Collaborative robots, which are used in industrial automation, depend on foundational software to guide them, writes Winston Leung, Senior Manager, QNX
The industrial automation sector has undergone a rapid transformation in recent years with the increased deployment of robotics technologies, and by 2033 the global market for robots with collaborative applications – also known as collaborative robots or cobots – is expected to reach around $23.5 billion. The sector has been at the forefront of the shift away from merely co-existent environments, towards more integrated and collaborative environments, in which machines work alongside humans in shared workspaces.
Manufacturers are increasingly using cobots in a bid to streamline assembly lines, welding, and material handling. According to a recent QNX study, 71% of global decision makers in engineering and manufacturing are already using robotics in their organisation, with 71% of those not currently using the technology planning to do so in the future.
Enhanced efficiency, reduced costs and increased precision are increasingly driving the industrial automation sector to explore how their existing infrastructure can be optimised through the deployment of these technologies. When doing so, however, manufacturers need to ensure that precision is paramount, as any deviation can lead to misalignments, defective products, and decreased overall workflow.
The shift to collaborative robotics technologies
Despite major advancements, robots still face many challenges – seeing, moving, and acting in ways that humans do naturally; while also having the benefit of programmability, repeatability, and robustness we expect from machines. This is where we are seeing a shift towards collaborative environments where robots and humans work side by side, engaging in more frequent and complex interactions.
But what developments are being made for cobots and how can they be adapted to enable robotic systems to operate safely in a collaborative environment while they perform their intended tasks?
Why foundational software is essential to modern computing
The operating system is core to ensuring the stability, performance and security of any computing environment. To ensure that these robots operate to its fullest potential, the OS must provide hard real-time determinism, guaranteeing precise timing and control over robotic actions. This orchestration helps facilitate the integration for which robotic applications are built upon. Safety and reliability are critical, which necessitates fault-tolerant mechanisms, including temporal and spatial isolation, to protect people from robots. Additionally, the OS must support advanced features such as machine learning, sensor fusion, and AI-driven decision-making, allowing the robot to adapt and respond to human interactions in real-time.
By leveraging a real-time OS, manufacturers can unlock the full capabilities of collaborative robots, enhancing productivity, safety, and operational efficiency across the production floor.
Why functional safety is more critical than ever for robotics technologies
The increasing complexity of cobots demands advanced functional safety measures to ensure that robots operate safely in proximity to human workers, adapting to their movements in real-time. It’s not just a technical necessity; it’s the foundation of a safe work environment especially when operating in dynamic environments. Robust safety protocols are critical for protecting workers, preventing accidents, and ensuring smooth operations. Furthermore, they build trust in automation, allowing industries to innovate and adopt new technologies.
Without functional safety, the risks associated with human-robot collaboration could slow progress and limit the potential of cobots. In this new era, functional safety isn’t just about protection; it’s a driver of innovation, enabling the safe exploration of new frontiers in automation while keeping human safety a top priority.
Collaborative robots could easily be integrated into any factory set-up, but there are still a few hurdles to clear before they become commonplace. For cobots to be deployed into existing infrastructure, manufacturers need to focus on safe design, proper integration, and ensuring software compatibility. Overcoming these challenges is essential for making cobots a seamless part of modern manufacturing.
Looking ahead, keeping up with safety standards like ISO 10218 and IEC 61508 will be crucial. ISO 10218 sets the rules for industrial robot safety, while IEC 61508 helps make sure electrical and electronic systems are built to be safe and reliable. By sticking to these guidelines, manufacturers can create robots and systems that are safer and less likely to fail, helping protect everyone working on the factory floor.
Robots offer significant potential for increased efficiency and accelerated production, but it’s people who bring creativity, flexibility, and a personal touch to the job. The real benefits show up when humans and robots work together and collaborate. By combining the accuracy of robots with human problem-solving and fresh ideas, companies can get more done while making the workplace safer and more engaging. Partnerships like these are shaping the future of manufacturing, where people and machines team up and make each other better.
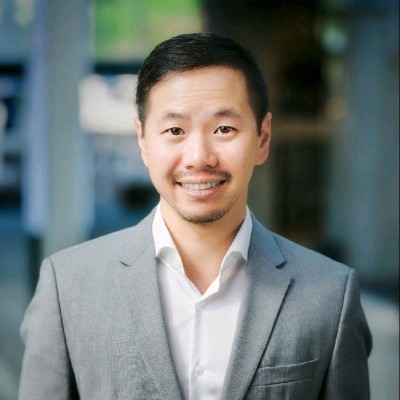
Winston is a Senior Manager at QNX with a proven track record of driving growth and innovation for global brands. He is passionate about harnessing data-driven strategies and creative solutions, achieve impactful, measurable results.
There’s plenty of other editorial on our sister site, Electronic Specifier! Or you can always join in the conversation by visiting our LinkedIn page.